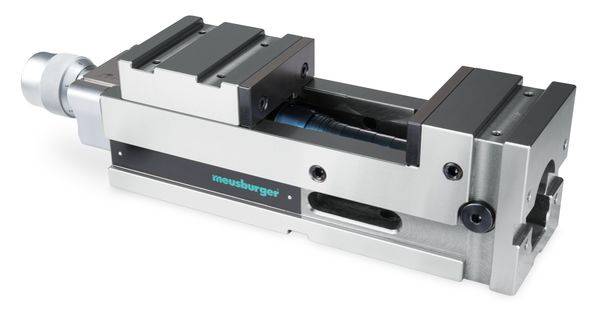
Clamping technology
We can offer suitable clamping devices for every application or task.
Here are some examples:
– Precision Vices
o Hydraulic
o Pneumatic
– Clamping modules
– Centering clamp
– Multifunction clamp
– Pneumatic clamping technology
– Short-stroke clamping elements
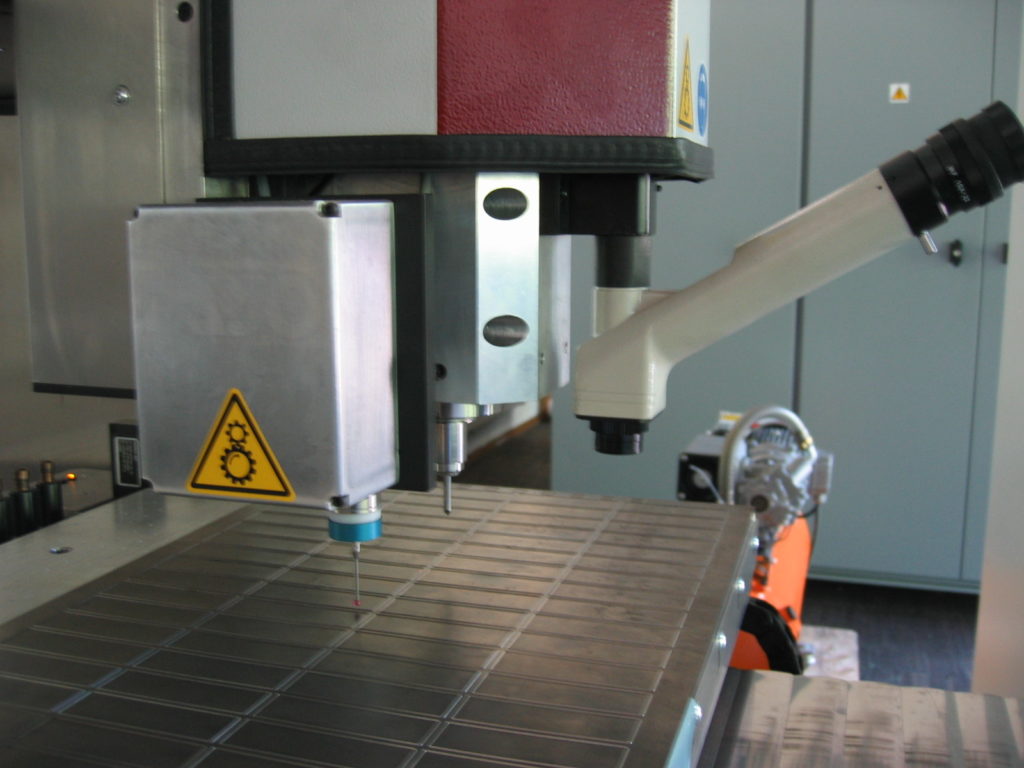
Centering microscope
Applications may require machining quality to be checked through a microscope before the workpiece is removed from the machine.
A good example here is the processing or sharpening and centering of cutting and stamping sheets.
The microscope can be picked up via the collet holder and the milling spindle.
The microscope has a built-in reticle and crosshairs.
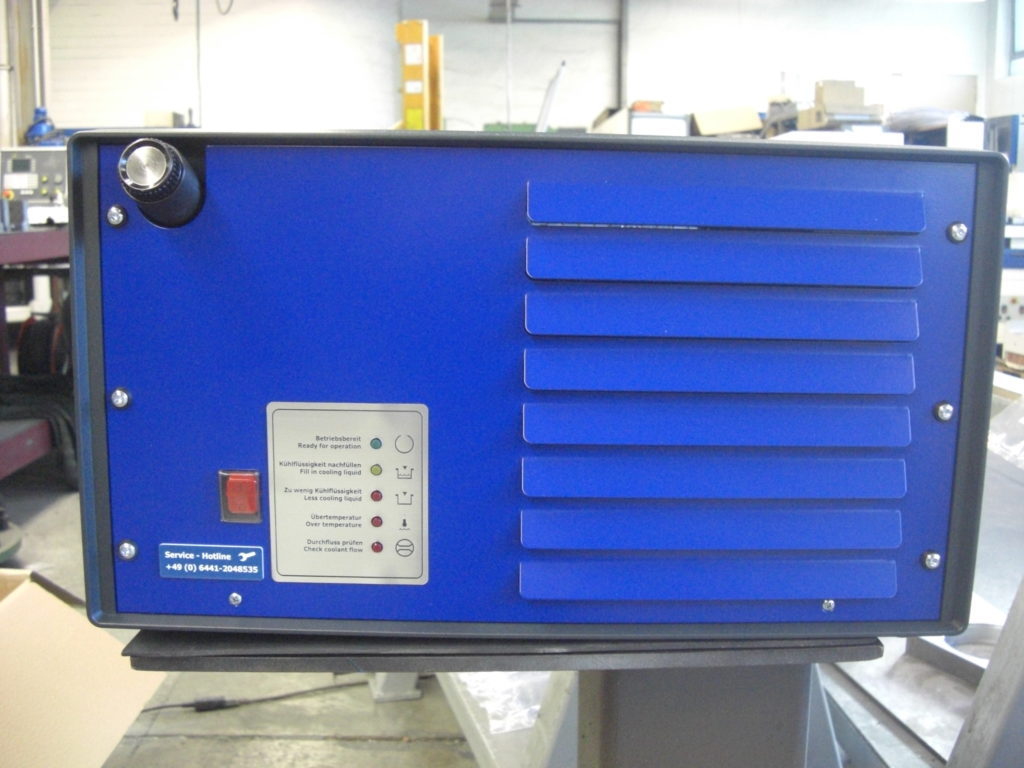
Increased temperature stability
Applications that require the highest precision require special measures in terms of temperature stability.
A good example here is the cooling of vacuum systems to prevent or counteract an expansion of the entire system over the temperature stability in the range of +/- 0.1k temperature hysteresis.
The same applies to milling spindles.
Again, the expansion of the spindle can be counteracted by an increased temperature stability.
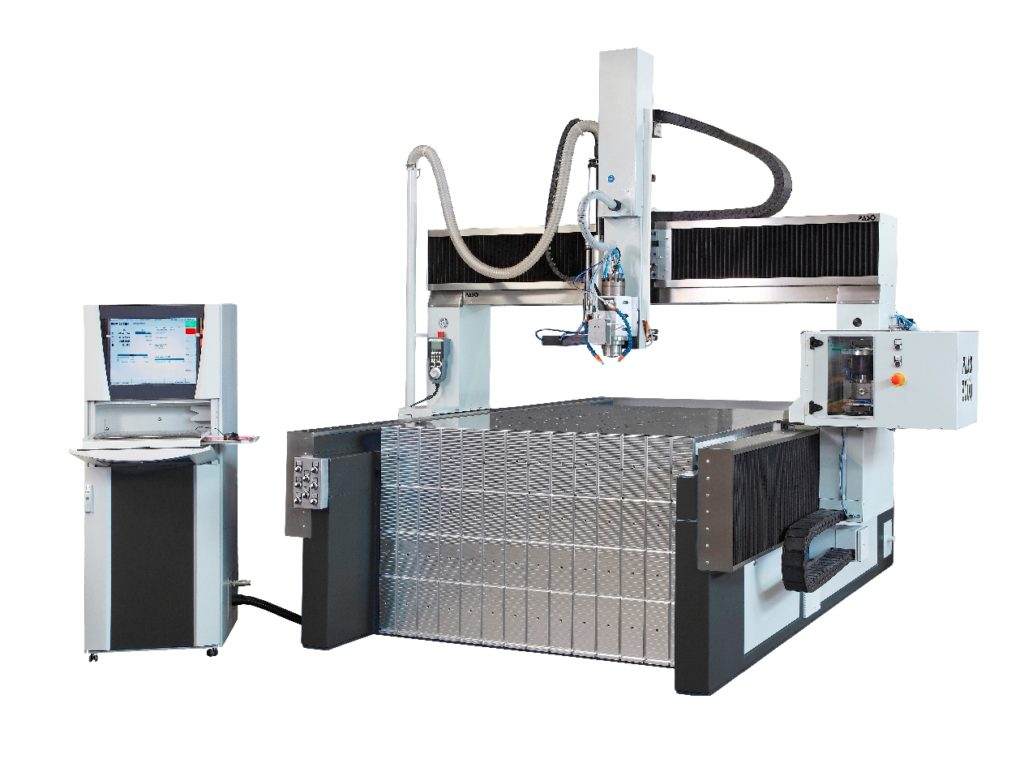
Front-side clamping
– by the front-side clamping you have the opportunity
Components that are higher than the portal passage, on the front to stretch
– possible width of the components, from 1000 to 1500mm x 100mm
– An assembly of the components is possible via grooves and tapped holes
– Material: aluminum
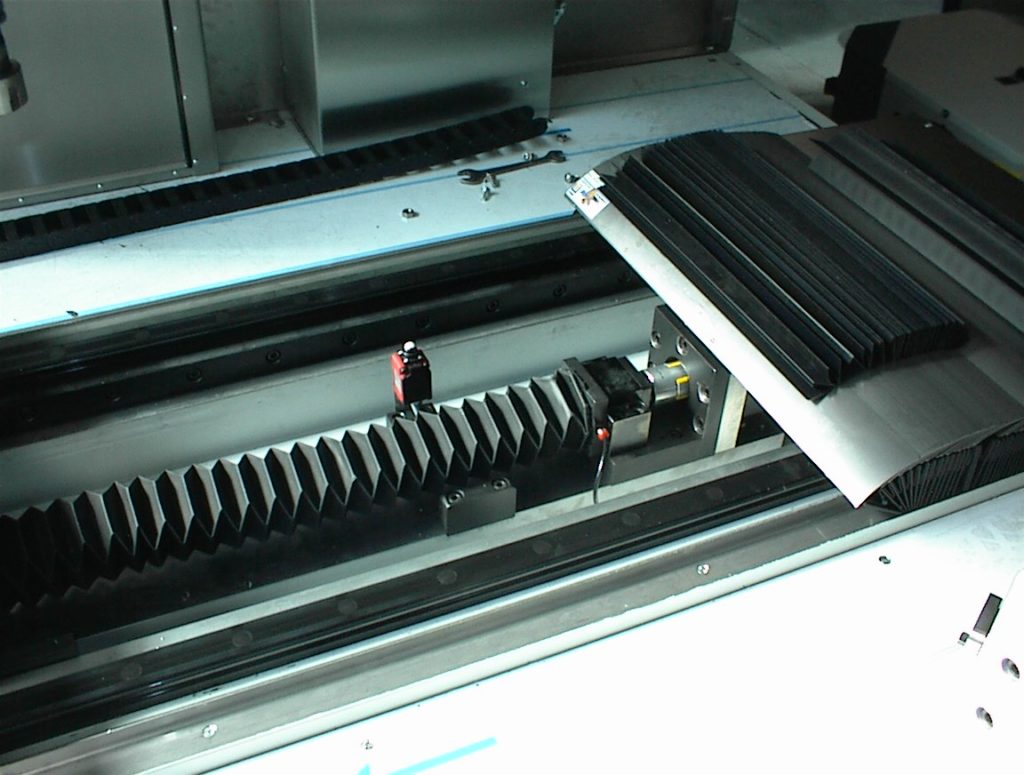
Option green processing
Abrasive materials, such as graphite or high-performance ceramics require special measures to protect the mechanics.
Here it is not just done with the fact that guide systems and ball screws are protected with bellows.
Our Option includes:
• black chromed guide systems
• sharp-edged holes in the guide system, thus no dirty edges after inserting the brass caps
• Guide carriage with K1 and 2 x rubber and extra thick steel scrapers each
• special internal scrapers
• Ball screw drive with contour wiper
• additional protection of ball screws with circumferential bellows
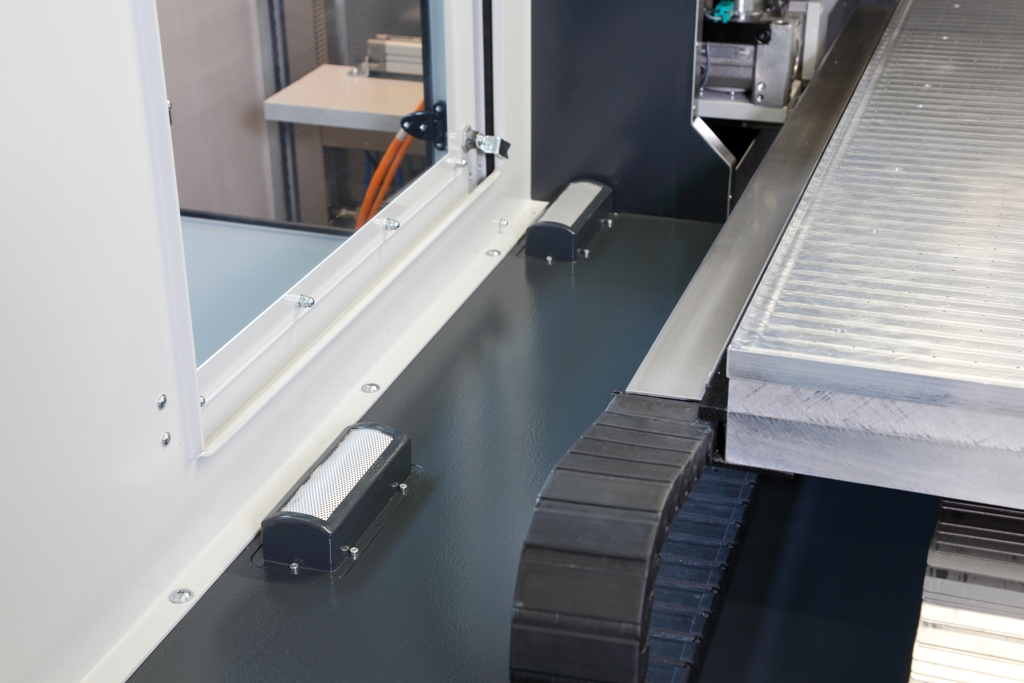
Option Climate
Market requirements with regard to precision in milling operations increase from year to year.
Whether it’s in tool and mould making,
micro-machining or medical technology, tolerances are getting increasingly tighter.
The demands made on machine technology are
therefore also more complex and costly.
High-precision drive and control technology in conjunction with precision guides are certainly the basis for precision manufacturing but regrettably they are not always the perfect solution.
All users are aware of the issue of temperature drift on processing machines in their day-to-day work, especially with the precision manufacturing of parts with a tight tolerance and this is often a problem that is very difficult to solve.
There are many approaches both inside and outside the machine to control this temperature fluctuation.
On the one hand, machines for precision manufacturing are installed in air-conditioned rooms or temperature tables in the control system should compensate for the geometric shifts; others try to imply that they have a stable temperature through the use of appropriate base materials, such as granite, and are therefore resistant to fluctuations in the ambient temperature.
It is often forgotten that the axis guide systems and their powertrains are still made of steel and firmly fixed to the base.
Highs and lows may occur rather than stable positioning and traversing movements on the condition that the body should remain stable and the guide systems should be subject to unavoidable linear expansion.
The other option of stabilising the ambient conditions is costly and time-consuming.
A further aspect of temperature drift is the heat sources within the machine.
There are approaches and solutions here that partially provide these heat sources with cooling systems at various points, such as milling spindles, driven nuts, etc., but do not detect the entire machine body.
PASO is taking the opposite approach with its latest development.
he machine itself is air-conditioned so there is no need for the machine environment to be air-conditioned or empirically determined compensation tables to offset the shifts.
The basis for this is a climate system with a heating and cooling function that is integrated into the machine.
The entire machine body and working area are maintained at a constant temperature using sophisticated air and cooling channels.
It’s not just during the day that an increase in temperature is eliminated but the machine also remains at a constant temperature overnight and at the weekend if the room temperature drops. A static shift in the machine geometry as the greatest unknown factor is therefore ruled out and the machine requires no time-consuming warm-up phases.
Initial experiences with the HSC1250, as well as and specifically under heavily fluctuating ambient temperatures, demonstrate the accuracy of this approach and are a further example of the fact that PASO has focussed on the demands of the market for many years and has reacted to its requirements with innovative solutions. This once again underlines PASO’s achievement potential and the focus of the business since its inception, incorporated into the corporate philosophy, is to supply its customers with a project-based solution rather than an off-the-peg standard machine.
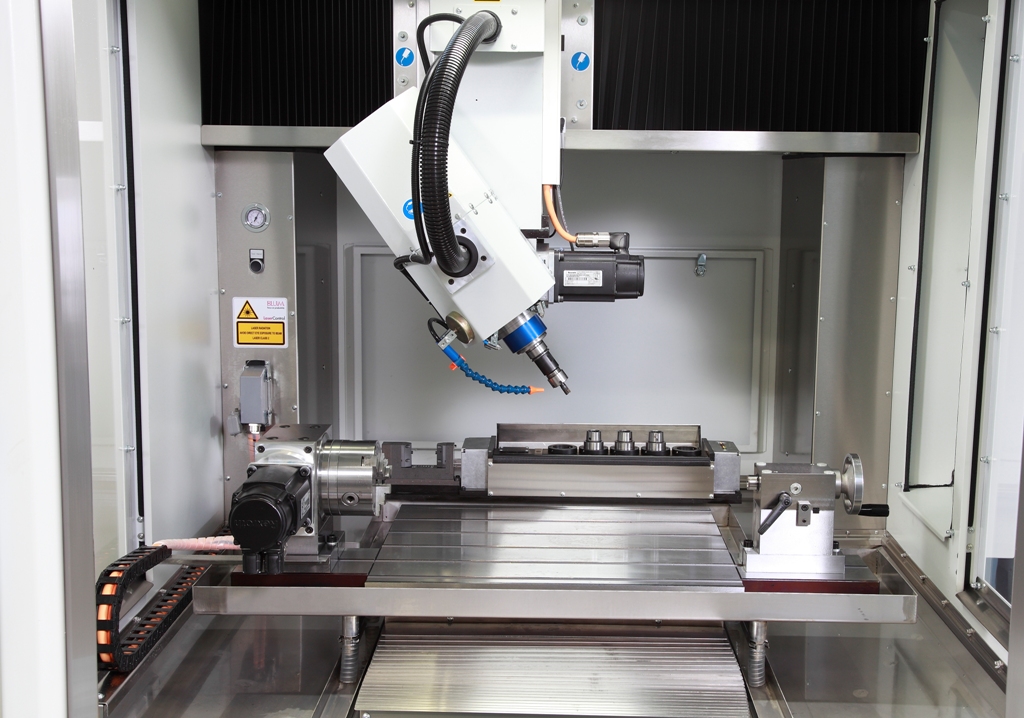
Wet processing option
Applications and machining tasks can make it necessary to resort to wet machining for strategic or economic reasons. Irrespective of this, there is currently a trend towards wet processing. Dry machining and MQL is problematic with high-temperature alloys or titanium. With these materials, the cooling lubricant is required to transport the heat away from the machining zone. In addition, high-pressure cooling is also required in many cases to optimize chip breaking at the cutting edge. Paso offers various solutions here: • In the simplest form and design, a stainless steel pan is mounted on the base plate of the machine. Circumferential drainage channels on the machine table with transition to the trough of the base plate bring the liquid through integrated sieves into the collection container. A submersible pump transports the liquid in a circuit.
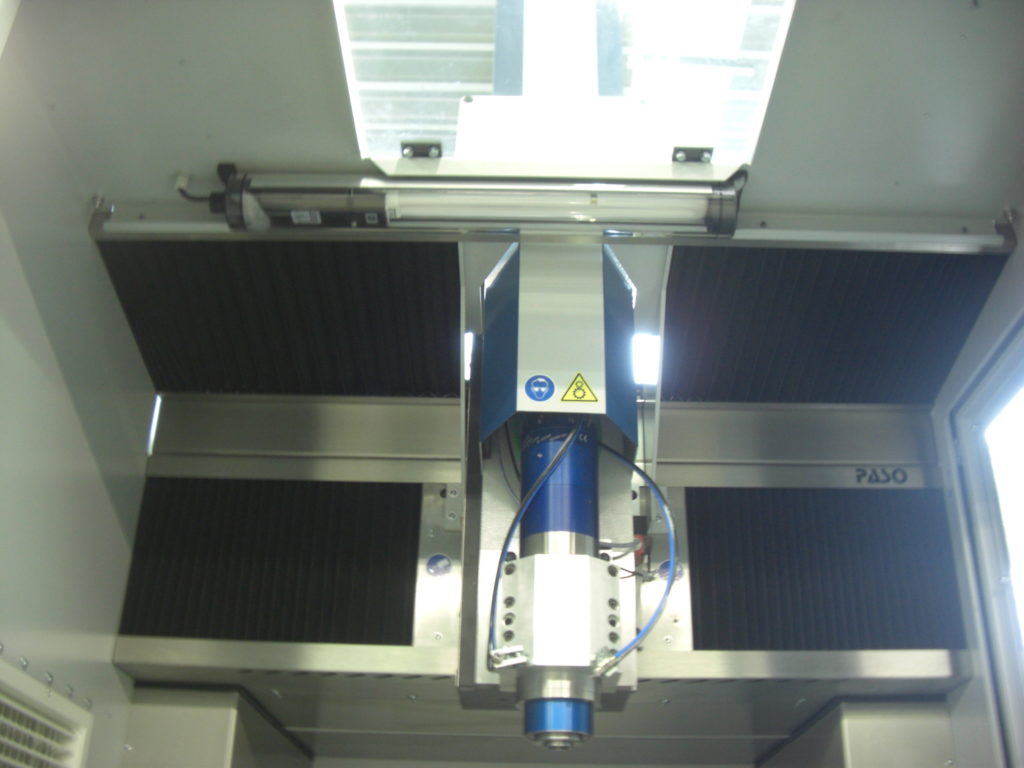
Option Protected
Applications and machining tasks may require the enclosure to be completely closed. This z. B. when processing abrasive materials such. B. graphite or high-performance ceramics. Here, the upper area, the “roof” of the housing, is meant in particular. Paso offers appropriate solutions here:
• Completely closed housing with additional bellows in the area of the machine roof
• Overpressure ventilation of the guide systems
• Preparation for a targeted flow of air within the enclosure using the “suck & blow” principle. This principle creates a negative pressure within the processing area and all chips and dust are sucked away by a corresponding suction device.
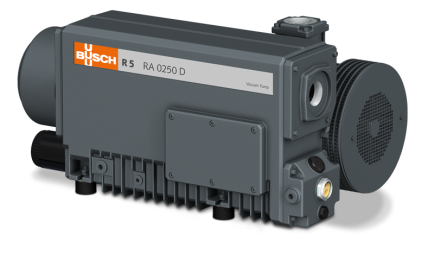
Vacuum Units
For holding workpieces, for the processing of vacuum technology is used.
The complete system consists of the actual vacuum system, the vacuum table and the vacuum unit.
The vacuum unit is usually oil-lubricated rotary vane vacuum pumps.
Depending on the work areas of the vacuum systems and the required nominal suction capacity, Paso offers the optimal solutions.